By NCC floor grinder and industrial vacuum
11/17/2011 http://www.floorshotblaster.com
There is much to consider when you buy your next piece of surface preparation equipment. Yet, there are ways to save time and money and to reduce the possibility of buying the wrong equipment.
When it's time to buy surface preparation equipment, first try to define the applications. While this sounds simple, overlooking this step can lead to poor production rates, higher labor costs, and frustrated workers. Concrete surfaces can have many different materials applied to them. Some of these are: existing coatings, cementitious overlays, rubber membranes, tile, carpet, and adhesives.
The age of the concrete surface is also important. Older floors may have been subjected to years of abuse, accumulated dirt, oil, and grease, all of which can affect which preparation process you use. Previous coverings (such as tile or glue-down carpet) may have been removed, leaving behind mastics and glues.
Older floors are usually harder, since hardening occurs throughout the life of the floor (at least for the first 100 years). New floors may have curing compounds on the surface.
With all of these variables, the applications can vary significantly within even a few inches. Remember that the new material being applied to the surface, if any, will influence the final preparation process as well. Thin materials such as urethanes, clear sealers, and clear coatings require a smoother, less aggressive profile.
The prepared area must be able to accept adhesion of a coating and provide the right amount of profile that will be hidden by the thickness of the coating. Thicker and cementitious materials require a more aggressive profile.
To date, there is no single process that can do all applications. So, breaking down the applications into two main categories of bulk material removal and final preparation will help. “Ooey, gooey, thick and chewy” substances are bulk materials you need to remove before final diamond-grinding or shotblasting. “Thin, hard, and cementitious” products can be a onestep process with diamond-grinding and/or shotblasting. The accompanying table is an excellent tool for determining which process is best and when to use it.
Removal processes
The bulk material removal processes are scarifying, scraping, and slicing. Scarifying is a mechanical preparation process that utilizes a drum with cutters mounted onto a horizontal shaft. The drum rotates, and the cutters strike the work surface first, and then the shafts strike the inner diameter of the cutters. This creates a hammer and chisel effect, chipping or scarring the concrete surface. There are a variety of cutters for different materials. Applications include removing thick lines, thermoplastic coatings, rubber membranes, and latex adhesives.
Scraping is a simple process that works on down force per square inch and surface feet per minute to keep the blade under the material being removed. It is ideal for removing VCT tile, carpet, rubber tile, adhesives, and thick failing epoxy.
Slicing works on exactly the same principle as scraping.But instead of using blades, it incorporates a carbide insert that is rotated on a disc. Applications include removing rubber membranes, latex adhesives, and thick epoxy coatings.
Prep processes
The final preparation processes are diamond grinding/polishing and shotblasting. Diamond grinding utilizes natural and synthetic diamonds introduced into a metal matrix. As the diamond travels over the work surface, it compresses and micro-fractures the surface. Once the diamond micro-fractures and/or metal matrix wears away, the diamond falls out of the matrix and is replaced by a new diamond. This process is repeated until the matrix is gone.
Selecting the correct bond hardness of the matrix is critical to production and tool life. The number one mistake made when buying diamond grinding equipment is not selecting the right bond hardness. The manufacturer should have a selection of bonds to work on different hardnesses of concrete. Generally, use a hard bond for soft materials and a soft bond for hard materials.
There is much to consider when you buy your next piece of surface preparation equipment. Yet, there are ways to save time and money and to reduce the possibility of buying the wrong equipment.
When it's time to buy surface preparation equipment, first try to define the applications. While this sounds simple, overlooking this step can lead to poor production rates, higher labor costs, and frustrated workers. Concrete surfaces can have many different materials applied to them. Some of these are: existing coatings, cementitious overlays, rubber membranes, tile, carpet, and adhesives.
The age of the concrete surface is also important. Older floors may have been subjected to years of abuse, accumulated dirt, oil, and grease, all of which can affect which preparation process you use. Previous coverings (such as tile or glue-down carpet) may have been removed, leaving behind mastics and glues.
Older floors are usually harder, since hardening occurs throughout the life of the floor (at least for the first 100 years). New floors may have curing compounds on the surface.
With all of these variables, the applications can vary significantly within even a few inches. Remember that the new material being applied to the surface, if any, will influence the final preparation process as well. Thin materials such as urethanes, clear sealers, and clear coatings require a smoother, less aggressive profile.
The prepared area must be able to accept adhesion of a coating and provide the right amount of profile that will be hidden by the thickness of the coating. Thicker and cementitious materials require a more aggressive profile.
To date, there is no single process that can do all applications. So, breaking down the applications into two main categories of bulk material removal and final preparation will help. “Ooey, gooey, thick and chewy” substances are bulk materials you need to remove before final diamond-grinding or shotblasting. “Thin, hard, and cementitious” products can be a onestep process with diamond-grinding and/or shotblasting. The accompanying table is an excellent tool for determining which process is best and when to use it.
Removal processes
The bulk material removal processes are scarifying, scraping, and slicing. Scarifying is a mechanical preparation process that utilizes a drum with cutters mounted onto a horizontal shaft. The drum rotates, and the cutters strike the work surface first, and then the shafts strike the inner diameter of the cutters. This creates a hammer and chisel effect, chipping or scarring the concrete surface. There are a variety of cutters for different materials. Applications include removing thick lines, thermoplastic coatings, rubber membranes, and latex adhesives.
Scraping is a simple process that works on down force per square inch and surface feet per minute to keep the blade under the material being removed. It is ideal for removing VCT tile, carpet, rubber tile, adhesives, and thick failing epoxy.
Slicing works on exactly the same principle as scraping.But instead of using blades, it incorporates a carbide insert that is rotated on a disc. Applications include removing rubber membranes, latex adhesives, and thick epoxy coatings.
Prep processes
The final preparation processes are diamond grinding/polishing and shotblasting. Diamond grinding utilizes natural and synthetic diamonds introduced into a metal matrix. As the diamond travels over the work surface, it compresses and micro-fractures the surface. Once the diamond micro-fractures and/or metal matrix wears away, the diamond falls out of the matrix and is replaced by a new diamond. This process is repeated until the matrix is gone.
Selecting the correct bond hardness of the matrix is critical to production and tool life. The number one mistake made when buying diamond grinding equipment is not selecting the right bond hardness. The manufacturer should have a selection of bonds to work on different hardnesses of concrete. Generally, use a hard bond for soft materials and a soft bond for hard materials.
There is much to consider when you buy your next piece of surface preparation equipment. Yet, there are ways to save time and money and to reduce the possibility of buying the wrong equipment.
When it's time to buy surface preparation equipment, first try to define the applications. While this sounds simple, overlooking this step can lead to poor production rates, higher labor costs, and frustrated workers. Concrete surfaces can have many different materials applied to them. Some of these are: existing coatings, cementitious overlays, rubber membranes, tile, carpet, and adhesives.
The age of the concrete surface is also important. Older floors may have been subjected to years of abuse, accumulated dirt, oil, and grease, all of which can affect which preparation process you use. Previous coverings (such as tile or glue-down carpet) may have been removed, leaving behind mastics and glues.
Older floors are usually harder, since hardening occurs throughout the life of the floor (at least for the first 100 years). New floors may have curing compounds on the surface.
With all of these variables, the applications can vary significantly within even a few inches. Remember that the new material being applied to the surface, if any, will influence the final preparation process as well. Thin materials such as urethanes, clear sealers, and clear coatings require a smoother, less aggressive profile.
The prepared area must be able to accept adhesion of a coating and provide the right amount of profile that will be hidden by the thickness of the coating. Thicker and cementitious materials require a more aggressive profile.
To date, there is no single process that can do all applications. So, breaking down the applications into two main categories of bulk material removal and final preparation will help. “Ooey, gooey, thick and chewy” substances are bulk materials you need to remove before final diamond-grinding or shotblasting. “Thin, hard, and cementitious” products can be a onestep process with diamond-grinding and/or shotblasting. The accompanying table is an excellent tool for determining which process is best and when to use it.
Removal processes
The bulk material removal processes are scarifying, scraping, and slicing. Scarifying is a mechanical preparation process that utilizes a drum with cutters mounted onto a horizontal shaft. The drum rotates, and the cutters strike the work surface first, and then the shafts strike the inner diameter of the cutters. This creates a hammer and chisel effect, chipping or scarring the concrete surface. There are a variety of cutters for different materials. Applications include removing thick lines, thermoplastic coatings, rubber membranes, and latex adhesives.
Scraping is a simple process that works on down force per square inch and surface feet per minute to keep the blade under the material being removed. It is ideal for removing VCT tile, carpet, rubber tile, adhesives, and thick failing epoxy.
Slicing works on exactly the same principle as scraping.But instead of using blades, it incorporates a carbide insert that is rotated on a disc. Applications include removing rubber membranes, latex adhesives, and thick epoxy coatings.
Prep processes
The final preparation processes are diamond grinding/polishing and shotblasting. Diamond grinding utilizes natural and synthetic diamonds introduced into a metal matrix. As the diamond travels over the work surface, it compresses and micro-fractures the surface. Once the diamond micro-fractures and/or metal matrix wears away, the diamond falls out of the matrix and is replaced by a new diamond. This process is repeated until the matrix is gone.
Selecting the correct bond hardness of the matrix is critical to production and tool life. The number one mistake made when buying diamond grinding equipment is not selecting the right bond hardness. The manufacturer should have a selection of bonds to work on different hardnesses of concrete. Generally, use a hard bond for soft materials and a soft bond for hard materials.
There is much to consider when you buy your next piece of surface preparation equipment. Yet, there are ways to save time and money and to reduce the possibility of buying the wrong equipment.
When it's time to buy surface preparation equipment, first try to define the applications. While this sounds simple, overlooking this step can lead to poor production rates, higher labor costs, and frustrated workers. Concrete surfaces can have many different materials applied to them. Some of these are: existing coatings, cementitious overlays, rubber membranes, tile, carpet, and adhesives.
The age of the concrete surface is also important. Older floors may have been subjected to years of abuse, accumulated dirt, oil, and grease, all of which can affect which preparation process you use. Previous coverings (such as tile or glue-down carpet) may have been removed, leaving behind mastics and glues.
Older floors are usually harder, since hardening occurs throughout the life of the floor (at least for the first 100 years). New floors may have curing compounds on the surface.
With all of these variables, the applications can vary significantly within even a few inches. Remember that the new material being applied to the surface, if any, will influence the final preparation process as well. Thin materials such as urethanes, clear sealers, and clear coatings require a smoother, less aggressive profile.
The prepared area must be able to accept adhesion of a coating and provide the right amount of profile that will be hidden by the thickness of the coating. Thicker and cementitious materials require a more aggressive profile.
To date, there is no single process that can do all applications. So, breaking down the applications into two main categories of bulk material removal and final preparation will help. “Ooey, gooey, thick and chewy” substances are bulk materials you need to remove before final diamond-grinding or shotblasting. “Thin, hard, and cementitious” products can be a onestep process with diamond-grinding and/or shotblasting. The accompanying table is an excellent tool for determining which process is best and when to use it.
Removal processes
The bulk material removal processes are scarifying, scraping, and slicing. Scarifying is a mechanical preparation process that utilizes a drum with cutters mounted onto a horizontal shaft. The drum rotates, and the cutters strike the work surface first, and then the shafts strike the inner diameter of the cutters. This creates a hammer and chisel effect, chipping or scarring the concrete surface. There are a variety of cutters for different materials. Applications include removing thick lines, thermoplastic coatings, rubber membranes, and latex adhesives.
Scraping is a simple process that works on down force per square inch and surface feet per minute to keep the blade under the material being removed. It is ideal for removing VCT tile, carpet, rubber tile, adhesives, and thick failing epoxy.
Slicing works on exactly the same principle as scraping.But instead of using blades, it incorporates a carbide insert that is rotated on a disc. Applications include removing rubber membranes, latex adhesives, and thick epoxy coatings.
Prep processes
The final preparation processes are diamond grinding/polishing and shotblasting. Diamond grinding utilizes natural and synthetic diamonds introduced into a metal matrix. As the diamond travels over the work surface, it compresses and micro-fractures the surface. Once the diamond micro-fractures and/or metal matrix wears away, the diamond falls out of the matrix and is replaced by a new diamond. This process is repeated until the matrix is gone.
Selecting the correct bond hardness of the matrix is critical to production and tool life. The number one mistake made when buying diamond grinding equipment is not selecting the right bond hardness. The manufacturer should have a selection of bonds to work on different hardnesses of concrete. Generally, use a hard bond for soft materials and a soft bond for hard materials.
There is much to consider when you buy your next piece of surface preparation equipment. Yet, there are ways to save time and money and to reduce the possibility of buying the wrong equipment.
When it's time to buy surface preparation equipment, first try to define the applications. While this sounds simple, overlooking this step can lead to poor production rates, higher labor costs, and frustrated workers. Concrete surfaces can have many different materials applied to them. Some of these are: existing coatings, cementitious overlays, rubber membranes, tile, carpet, and adhesives.
The age of the concrete surface is also important. Older floors may have been subjected to years of abuse, accumulated dirt, oil, and grease, all of which can affect which preparation process you use. Previous coverings (such as tile or glue-down carpet) may have been removed, leaving behind mastics and glues.
Older floors are usually harder, since hardening occurs throughout the life of the floor (at least for the first 100 years). New floors may have curing compounds on the surface.
With all of these variables, the applications can vary significantly within even a few inches. Remember that the new material being applied to the surface, if any, will influence the final preparation process as well. Thin materials such as urethanes, clear sealers, and clear coatings require a smoother, less aggressive profile.
The prepared area must be able to accept adhesion of a coating and provide the right amount of profile that will be hidden by the thickness of the coating. Thicker and cementitious materials require a more aggressive profile.
To date, there is no single process that can do all applications. So, breaking down the applications into two main categories of bulk material removal and final preparation will help. “Ooey, gooey, thick and chewy” substances are bulk materials you need to remove before final diamond-grinding or shotblasting. “Thin, hard, and cementitious” products can be a onestep process with diamond-grinding and/or shotblasting. The accompanying table is an excellent tool for determining which process is best and when to use it.
Removal processes
The bulk material removal processes are scarifying, scraping, and slicing. Scarifying is a mechanical preparation process that utilizes a drum with cutters mounted onto a horizontal shaft. The drum rotates, and the cutters strike the work surface first, and then the shafts strike the inner diameter of the cutters. This creates a hammer and chisel effect, chipping or scarring the concrete surface. There are a variety of cutters for different materials. Applications include removing thick lines, thermoplastic coatings, rubber membranes, and latex adhesives.
Scraping is a simple process that works on down force per square inch and surface feet per minute to keep the blade under the material being removed. It is ideal for removing VCT tile, carpet, rubber tile, adhesives, and thick failing epoxy.
Slicing works on exactly the same principle as scraping.But instead of using blades, it incorporates a carbide insert that is rotated on a disc. Applications include removing rubber membranes, latex adhesives, and thick epoxy coatings.
Prep processes
The final preparation processes are diamond grinding/polishing and shotblasting. Diamond grinding utilizes natural and synthetic diamonds introduced into a metal matrix. As the diamond travels over the work surface, it compresses and micro-fractures the surface. Once the diamond micro-fractures and/or metal matrix wears away, the diamond falls out of the matrix and is replaced by a new diamond. This process is repeated until the matrix is gone.
Selecting the correct bond hardness of the matrix is critical to production and tool life. The number one mistake made when buying diamond grinding equipment is not selecting the right bond hardness. The manufacturer should have a selection of bonds to work on different hardnesses of concrete. Generally, use a hard bond for soft materials and a soft bond for hard materials.
There is much to consider when you buy your next piece of surface preparation equipment. Yet, there are ways to save time and money and to reduce the possibility of buying the wrong equipment.
When it's time to buy surface preparation equipment, first try to define the applications. While this sounds simple, overlooking this step can lead to poor production rates, higher labor costs, and frustrated workers. Concrete surfaces can have many different materials applied to them. Some of these are: existing coatings, cementitious overlays, rubber membranes, tile, carpet, and adhesives.
The age of the concrete surface is also important. Older floors may have been subjected to years of abuse, accumulated dirt, oil, and grease, all of which can affect which preparation process you use. Previous coverings (such as tile or glue-down carpet) may have been removed, leaving behind mastics and glues.
Older floors are usually harder, since hardening occurs throughout the life of the floor (at least for the first 100 years). New floors may have curing compounds on the surface.
With all of these variables, the applications can vary significantly within even a few inches. Remember that the new material being applied to the surface, if any, will influence the final preparation process as well. Thin materials such as urethanes, clear sealers, and clear coatings require a smoother, less aggressive profile.
The prepared area must be able to accept adhesion of a coating and provide the right amount of profile that will be hidden by the thickness of the coating. Thicker and cementitious materials require a more aggressive profile.
To date, there is no single process that can do all applications. So, breaking down the applications into two main categories of bulk material removal and final preparation will help. "Ooey, gooey, thick and chewy" substances are bulk materials you need to remove before final diamond-grinding or shotblasting. "Thin, hard, and cementitious" products can be a onestep process with diamond-grinding and/or shotblasting. The accompanying table is an excellent tool for determining which process is best and when to use it.
Removal processes
The bulk material removal processes are scarifying, scraping, and slicing. Scarifying is a mechanical preparation process that utilizes a drum with cutters mounted onto a horizontal shaft. The drum rotates, and the cutters strike the work surface first, and then the shafts strike the inner diameter of the cutters. This creates a hammer and chisel effect, chipping or scarring the concrete surface. There are a variety of cutters for different materials. Applications include removing thick lines, thermoplastic coatings, rubber membranes, and latex adhesives.
Scraping is a simple process that works on down force per square inch and surface feet per minute to keep the blade under the material being removed. It is ideal for removing VCT tile, carpet, rubber tile, adhesives, and thick failing epoxy.
Slicing works on exactly the same principle as scraping.But instead of using blades, it incorporates a carbide insert that is rotated on a disc. Applications include removing rubber membranes, latex adhesives, and thick epoxy coatings.
Prep processes
The final preparation processes are diamond grinding/polishing and shotblasting. Diamond grinding utilizes natural and synthetic diamonds introduced into a metal matrix. As the diamond travels over the work surface, it compresses and micro-fractures the surface. Once the diamond micro-fractures and/or metal matrix wears away, the diamond falls out of the matrix and is replaced by a new diamond. This process is repeated until the matrix is gone.
Selecting the correct bond hardness of the matrix is critical to production and tool life. The number one mistake made when buying diamond grinding equipment is not selecting the right bond hardness. The manufacturer should have a selection of bonds to work on different hardnesses of concrete. Generally, use a hard bond for soft materials and a soft bond for hard materials.
There is much to consider when you buy your next piece of surface preparation equipment. Yet, there are ways to save time and money and to reduce the possibility of buying the wrong equipment.
When it's time to buy surface preparation equipment, first try to define the applications. While this sounds simple, overlooking this step can lead to poor production rates, higher labor costs, and frustrated workers. Concrete surfaces can have many different materials applied to them. Some of these are: existing coatings, cementitious overlays, rubber membranes, tile, carpet, and adhesives.
The age of the concrete surface is also important. Older floors may have been subjected to years of abuse, accumulated dirt, oil, and grease, all of which can affect which preparation process you use. Previous coverings (such as tile or glue-down carpet) may have been removed, leaving behind mastics and glues.
Older floors are usually harder, since hardening occurs throughout the life of the floor (at least for the first 100 years). New floors may have curing compounds on the surface.
With all of these variables, the applications can vary significantly within even a few inches. Remember that the new material being applied to the surface, if any, will influence the final preparation process as well. Thin materials such as urethanes, clear sealers, and clear coatings require a smoother, less aggressive profile.
The prepared area must be able to accept adhesion of a coating and provide the right amount of profile that will be hidden by the thickness of the coating. Thicker and cementitious materials require a more aggressive profile.
To date, there is no single process that can do all applications. So, breaking down the applications into two main categories of bulk material removal and final preparation will help. "Ooey, gooey, thick and chewy" substances are bulk materials you need to remove before final diamond-grinding or shotblasting. "Thin, hard, and cementitious" products can be a onestep process with diamond-grinding and/or shotblasting. The accompanying table is an excellent tool for determining which process is best and when to use it.
Removal processes
The bulk material removal processes are scarifying, scraping, and slicing. Scarifying is a mechanical preparation process that utilizes a drum with cutters mounted onto a horizontal shaft. The drum rotates, and the cutters strike the work surface first, and then the shafts strike the inner diameter of the cutters. This creates a hammer and chisel effect, chipping or scarring the concrete surface. There are a variety of cutters for different materials. Applications include removing thick lines, thermoplastic coatings, rubber membranes, and latex adhesives.
Scraping is a simple process that works on down force per square inch and surface feet per minute to keep the blade under the material being removed. It is ideal for removing VCT tile, carpet, rubber tile, adhesives, and thick failing epoxy.
Slicing works on exactly the same principle as scraping.But instead of using blades, it incorporates a carbide insert that is rotated on a disc. Applications include removing rubber membranes, latex adhesives, and thick epoxy coatings.
Prep processes
The final preparation processes are diamond grinding/polishing and shotblasting. Diamond grinding utilizes natural and synthetic diamonds introduced into a metal matrix. As the diamond travels over the work surface, it compresses and micro-fractures the surface. Once the diamond micro-fractures and/or metal matrix wears away, the diamond falls out of the matrix and is replaced by a new diamond. This process is repeated until the matrix is gone.
Selecting the correct bond hardness of the matrix is critical to production and tool life. The number one mistake made when buying diamond grinding equipment is not selecting the right bond hardness. The manufacturer should have a selection of bonds to work on different hardnesses of concrete. Generally, use a hard bond for soft materials and a soft bond for hard materials.
NCC floor grinder and industrial vacuum
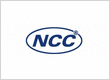
NCC Machine Co., Ltd. is a leading manufacture of floor surface preparation machines, industrial vacuum cleaners and cleaning machines. Our main products are floor grinder, floor grinding machine, shot blasting machine, industrial vacuum cleaner, concrete grinder, diamond grinder, disc grinder, disc…